Actuators are used in directional control valves to provide the necessary force and motion to control the position of the valve spool or piston.
The main reasons for using actuators in directional control valves include:
1. Valve Positioning: Actuators allow the valve spool or piston to be precisely positioned, which is crucial for controlling the flow of fluid through the valve. This precise positioning enables the valve to direct the fluid flow in the desired direction.
2. Mechanical Actuation: Actuators provide the mechanical force required to physically move the valve spool or piston. This is necessary as the fluid pressures alone may not be sufficient to reliably position the Extension Stem Butterfly Valve .
3. Remote Control: Actuators allow the valve to be controlled remotely, rather than requiring manual operation. This is useful in applications where the valve is located in a difficult-to-access area or where remote control is preferred for safety or efficiency reasons.
4. Automation: Actuators enable the integration of directional control valves into automated systems, such as industrial machinery or process control applications. The actuators can be controlled by electrical signals, pneumatic pressures, or other control inputs to automate the operation of the valve.
5. Increased Responsiveness: Actuators can provide fast and precise movement of the valve spool or piston, allowing for rapid changes in fluid flow direction and improved system responsiveness.
The specific type of actuator used (e.g., solenoid, pneumatic, hydraulic, or electric) depends on the application requirements, such as the required force, speed, and control mechanisms.
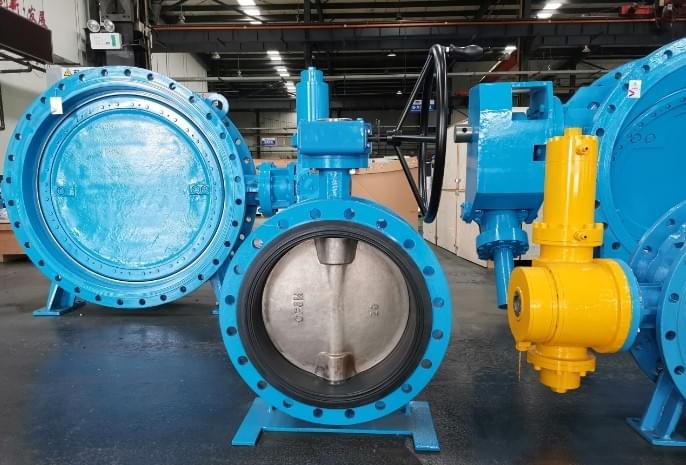