Spunbond and meltblown are two different methods of producing nonwoven fabrics, and each has its own advantages and disadvantages depending on the intended use of the fabric.
Spunbond fabrics are produced by spinning and bonding continuous filaments of synthetic fibers. The resulting fabric is relatively strong, durable, and resistant to tearing, but may be less effective at blocking small particles such as bacteria and viruses. Spunbond fabrics are commonly used in applications such as geotextiles, agriculture, and furniture.
Meltblown fabrics, on the other hand, are produced by extruding molten thermoplastic polymers through a series of fine nozzles and then blowing the fibers onto a moving conveyor belt to form a random, nonwoven mat. Meltblown fabrics have very fine fibers, typically in the range of 0.5 to 5 microns, which make them highly effective at filtering small particles such as bacteria and viruses. Meltblown fabrics are commonly used in medical masks, air filters, and other applications where high levels of filtration are required.
In summary, the choice between spunbond and meltblown will depend on the specific application and the desired properties of the fabric. Spunbond may be more appropriate for applications where strength and durability are important, while meltblown may be more suitable for applications where filtration is a critical factor.
What is PP S Spunbond Machin technology?
PP S spunbond machine technology is a manufacturing process used to produce spunbond nonwoven fabrics using polypropylene (PP) as the raw material.
The process involves several steps, including:
- Extrusion: The PP resin is melted and extruded through a spinneret to form continuous filaments.
- Quenching: The filaments are cooled rapidly by passing them through a quenching chamber.
- Bonding: The filaments are spread evenly and bonded together by applying heat and pressure.
- Finishing: The finished fabric is subjected to various finishing treatments to improve its properties, such as softness, water repellency, and flame resistance.
The technology used in PP S spunbond machines can vary depending on the specific manufacturer and design, but generally involves a combination of extrusion, quenching, bonding, and finishing processes. These machines can produce nonwoven fabrics in a range of widths, thicknesses, and densities, depending on the desired end use. China PP S Spunbond Machine supplier Spunbond nonwoven fabrics produced using PP S spunbond technology have a range of applications, including in the automotive, construction, agriculture, and healthcare industries.
Is spunbond polypropylene the same as meltblown?
Spunbond polypropylene and meltblown are two different types of nonwoven fabrics, although they are often used together in various applications, including in the production of face masks.
Spunbond polypropylene is produced by spinning and bonding continuous filaments of synthetic fibers. The resulting fabric is relatively strong, durable, and resistant to tearing, but may be less effective at blocking small particles such as bacteria and viruses.
Meltblown, on the other hand, is produced by extruding molten thermoplastic polymers through a series of fine nozzles and then blowing the fibers onto a moving conveyor belt to form a random, nonwoven mat. Meltblown fabrics have very fine fibers, typically in the range of 0.5 to 5 microns, which make them highly effective at filtering small particles such as bacteria and viruses.
In the production of face masks, a combination of spunbond polypropylene and meltblown is often used. The outer layer is typically made of spunbond polypropylene, which provides strength and durability, while the inner layer is made of meltblown, which provides effective filtration of small particles.
In summary, spunbond polypropylene and meltblown are two different types of nonwoven fabrics, with different properties and characteristics, but they are often used together in applications where both strength and filtration are required.
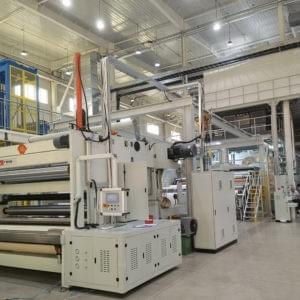