Manufacturers employ various strategies to address potential issues like load swing, sway, and rotation in industrial crane designs.
Here are some of the key approaches:
Anti-Sway Control Systems:
Cranes can be equipped with advanced anti-sway control algorithms and sensors that detect and counteract load swing and sway.
These systems use real-time feedback from load sensors, encoders, and accelerometers to quickly adjust the crane's motions and damp out any unwanted load movements.
The control system can make automatic adjustments to the hoist, trolley, and bridge speeds to minimize load oscillations and maintain the load in a stable, centered position.
Trolley and Hoist Positioning:
Strategic placement and positioning of the trolley and hoist can help minimize the potential for load swing and rotation.
Offset or asymmetric trolley designs can help counteract natural tendencies for load swing or rotation.
Precise control of the hoist's lowering and lifting speeds, as well as the trolley's acceleration and deceleration, can also help manage load dynamics.
Operator Assist Features:
Crane control systems can incorporate operator-assist functions that guide the operator in maintaining load stability.
These features can include dynamic load positioning indicators, industrial crane sway-limiting controls, and automated load-centering routines.
By providing real-time feedback and semi-autonomous control capabilities, these features help the operator minimize unwanted load movements.
Structural Design Optimization:
The crane's structural design, including the bridge, trolley, and hoist, can be optimized to minimize load swing and sway.
This may involve the use of finite element analysis, computational fluid dynamics, and other modeling techniques to simulate load dynamics and inform the structural design.
Factors like bridge stiffness, trolley weight distribution, and hoist suspension geometry can be engineered to reduce the potential for load instability.
Active Suspension Systems:
Some advanced crane designs incorporate active suspension systems that use actuators, sensors, and control algorithms to actively counteract load swing and sway.
These systems can rapidly adjust the hoist's suspension geometry or apply corrective forces to stabilize the load and maintain its position.
Damping Mechanisms:
Passive damping mechanisms, such as shock absorbers or pendulum-type devices, can be integrated into the crane's design to dissipate energy and reduce load oscillations.
These mechanisms help convert the kinetic energy of the load swing into heat, effectively damping out the unwanted movements.
By employing a combination of these strategies, manufacturers can address the challenges of load swing, sway, and rotation in industrial crane designs, ensuring safe, efficient, and precise material handling operations.
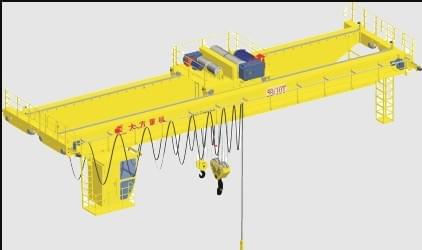